-
From Cézanne to the Césars: four French art and culture recommendations
Impressionist masterpieces in Aix-en-Provence, a stylish Louvre exhibition, and a crime series to watch
-
Photos: Paris exhibition explores what people do alone at home
Behind the curtain: L’Intime Expo takes a fascinating look at people's private lives
-
French art gallery exhibits paintings made by a two-year-old
The abstract creations are being displayed until next week
French crafts in focus: The art of cutting gems
France was once a hotbed for gem cutters but now Maison Piat is one of the few remaining companies offering this service
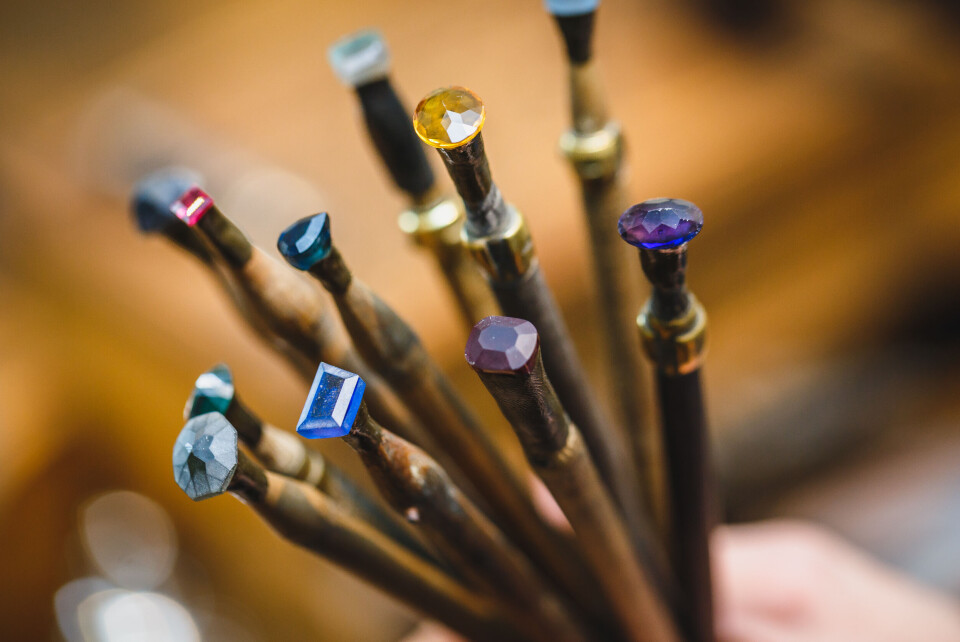
The Jura was once the centre of gem-cutting in Europe, with an estimated 8,000 skilled artisans (known as lapidaires) working in the heart of the mountains in 1920.
Like many other traditional crafts, competition from Asia means there are now very few workshops left: maybe fewer than 10 in France.
Maison Piat, established in 1983, is based in Paris and was set up by the son-in-law of a Jura gem-cutter who came to the capital in the early 20th century. It boasts five gem-cutters, who specialise in working centre gemstones from rough or cut stones.
In 2013, it obtained the label Entreprise du Patrimoine Vivant, for companies that use and develop traditional skills, and in 2020 it was the first in the coloured stones industry to get Responsible Jewellery Council certification, which ensures only ethically sourced gems are used.
Company spokeswoman Sarah Boidart said: “It is important that people are aware that cutting gems is a complex skill, which takes a lifetime to perfect.
“It has a long tradition in France and produces gems and jewellery of a very high quality.”
There is a distinction between lapidaires, who cut coloured stones, and diamantaires, who work only with diamonds.
The two can never take place in the same workshop as diamond microparticles could contaminate a coloured stone tool and risk cutting and damaging a precious stone.
“The art of lapidary is to maximise the reflection of light and produce a uniform colour that is the strongest the stone has to offer,” says Ms Boidart.
“Gems have different qual-ities. For example, when light hits a sapphire, it is refracted in two, producing the main colour, let us say blue, and a secondary colour, which could be a grey- or green-blue. The savoir-faire of the gem-cutter is the ability to choose the best part of the stone and then cut it to make sure the eye sees the most magnificent blue possible.
“It is a complex and technical art, learnt through experience. Each stone is different.”
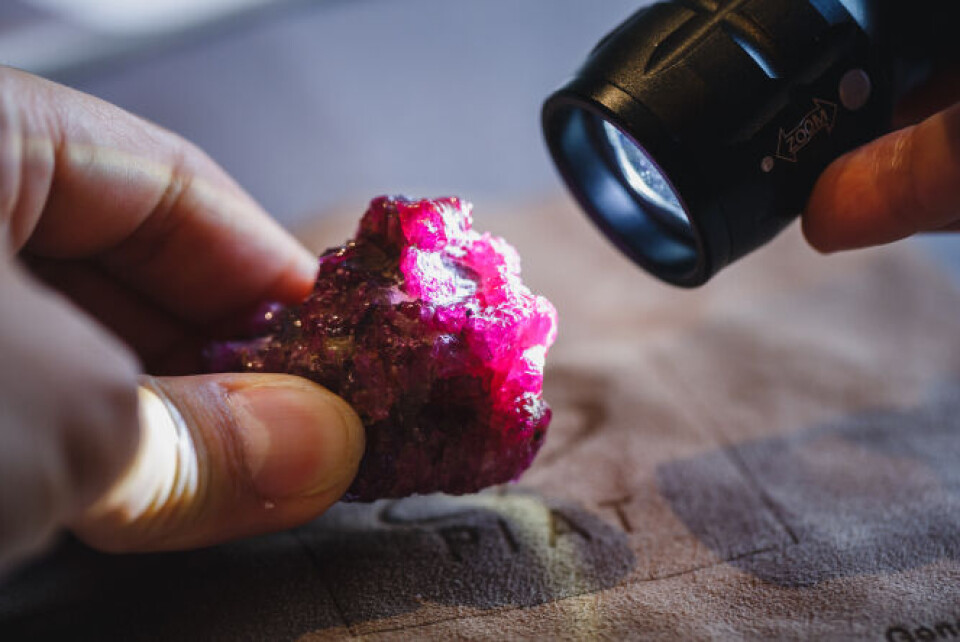
Usually, gem-cutters improve stones that have already been cut, but since it obtained Responsible Jewellery Council certification, Maison Piat has begun to work increasingly with rough stones.
These come from Moyo Gems, an ethical gemstone collaboration which works with female artisanal gem miners in Tanzania and Kenya.
The gems are sourced from mines which do not exploit or mistreat their workers, and are not involved in bribery or money-laundering. Working on rough gemstones is challenging and requires careful study of the stone first, as a lapidaire must produce the finest gems while minimising weight loss.
Read more: Crafts in focus: meet French weathervane-maker Thierry Soret
“First, the gem-cutter observes it from all sides, and in different lights throughout the day,” says Ms Boidart.
“They will look for any inclusions that might affect the clarity of the gem. They will put it into a small porcelain bowl of water to better identify the colour zones. In a rough stone, it is very rare that the colour will be consistent.
“This will help them decide where the pavilion, the name for the base of the gem, will be, which is where the colour is concentrated.” After this, a small area is polished to give a window into the interior of the stone, as they are often matt when raw.
The gem-cutter will then put it aside for several days before returning to it with fresh eyes, having given much thought to the different possible end results and, if it is very valuable, seeking advice from colleagues.
Only then will they decide how to treat the stone.
“They will produce the desired shape but make it larger than the end result, a bit like the first sketch made by a painter,” says Ms Boidart.
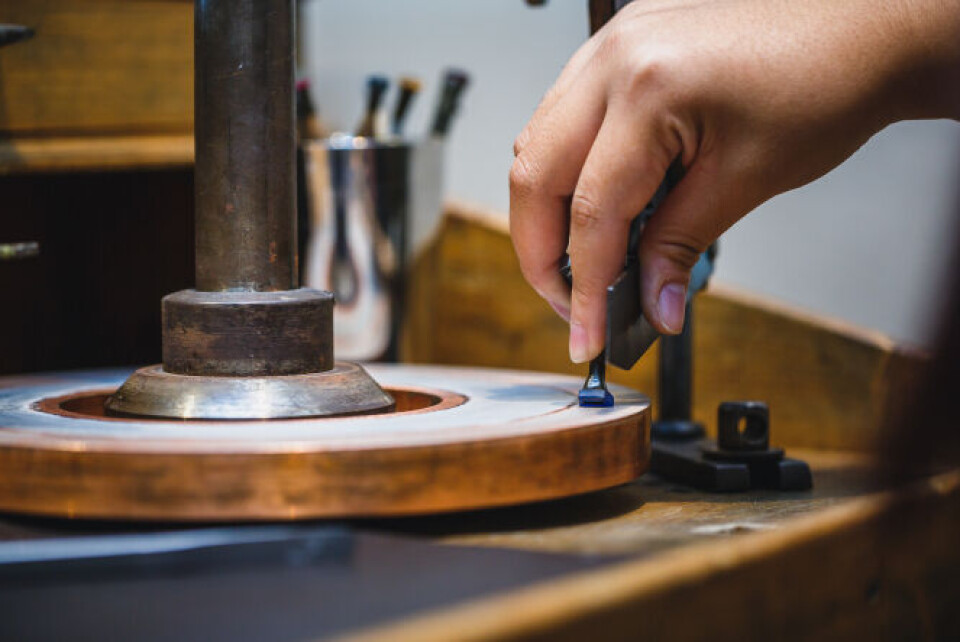
This could see 60-65% of the original weight shaved off, after which the gem-cutter will make sure there are no hidden imperfections. When satisfied, they attach the stone to a rod and first work on the top half of the stone, the crown, before moving down to the pavilion.
“Everything is done by eye,” says Ms Boidart.
“After, it must be polished so the stone reflects the light perfectly and reveals all its beauty through each of the facets.”
One stone can take a day to cut but sometimes it stretches to a week. If the gem is already cut, the process is similar but shorter. However, it requires careful calculation before cutting to avoid losing too much of the original weight.
Read more: French crafts in focus: clock and lock-maker
Different types of grindstone are used for each stage. For faceting, they are made from steel and diamond, and water runs over them constantly to regulate the temperature. For polishing, the grindstone is usually in pewter and covered with a mixture of diamond powder and oil.
This differs for certain stones: sapphires, for example, need a copper grindstone.
Emeralds require special treatment because they sometimes have mini-fractures (called les jardins in French)and the black paste from the oil and diamonds would leave traces in the minuscule marks.
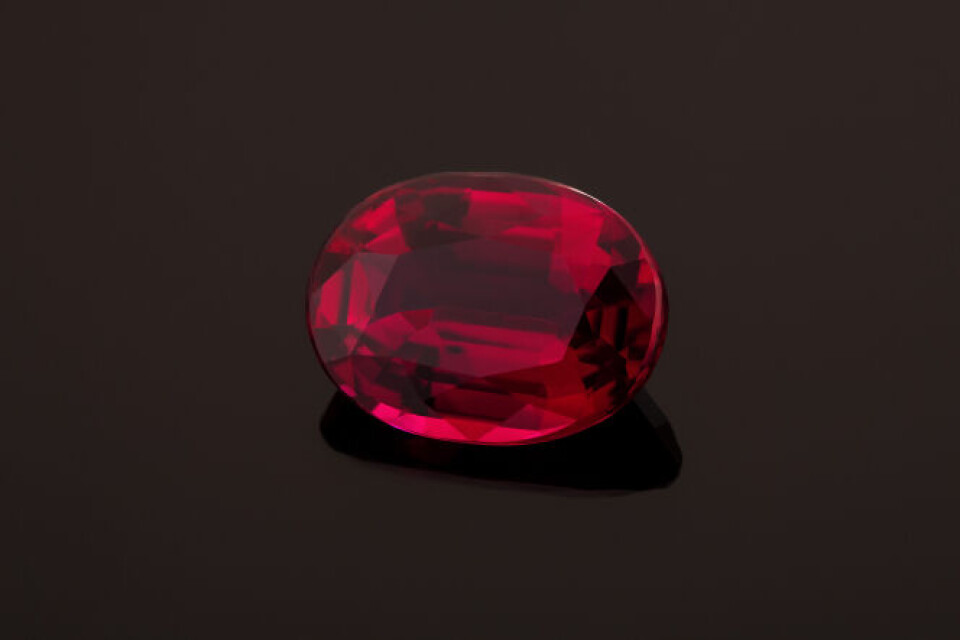
For that reason, the grindstone is made from a resin mixed with chromium, which is the element that colours the emerald green, and diamond powder.
This expertise dates back to the 16th and 17th centuries, when religious persecution saw Catholic artisans from Geneva chased across the border into France. When Swiss clock-makers introduced rubies into their mechanisms in 1700, work for gem-cutters increased.
Many worked on farms in the summer and were able to earn extra income from gems at home during long, hard winters when villages were isolated.
Though there are very few workshops left, there are still lapidaire training courses available in a handful of schools in France, including the Haute Ecole de Joaillerie in Paris and the Institut de Bijouterie de Saumur, Maine-et-Loire.
Maison Piat runs its own training programme, and welcomes apprentices studying the art of lapidary from other schools.
Related stories:
Rare gems found near Mont-Blanc shared with French town of Chamonix
300 luxury items up for auction as French customs sell seized goods
Omar Sy's Lupin most popular ever French show on Netflix