-
What makes France so French?
We take a look at five French traditions on the UNESCO 'intangible cultural heritage' list
-
'I helped restore French cathedrals as a female American stone cutter - despite prejudice'
Stella Cheng, who worked on the restoration of Notre-Dame Cathedral, faced sexism and racism
-
French woman named one of world’s best teachers
Céline Haller, inspired by English and US teaching methods, has gained recognition for revolutionising learning with hands-on projects and inclusivity
Discover the espadrille firm using French know-how and Queen’s face
Based in south-west France and still using traditional methods, the company made headlines recently for its offbeat tribute to the British monarch
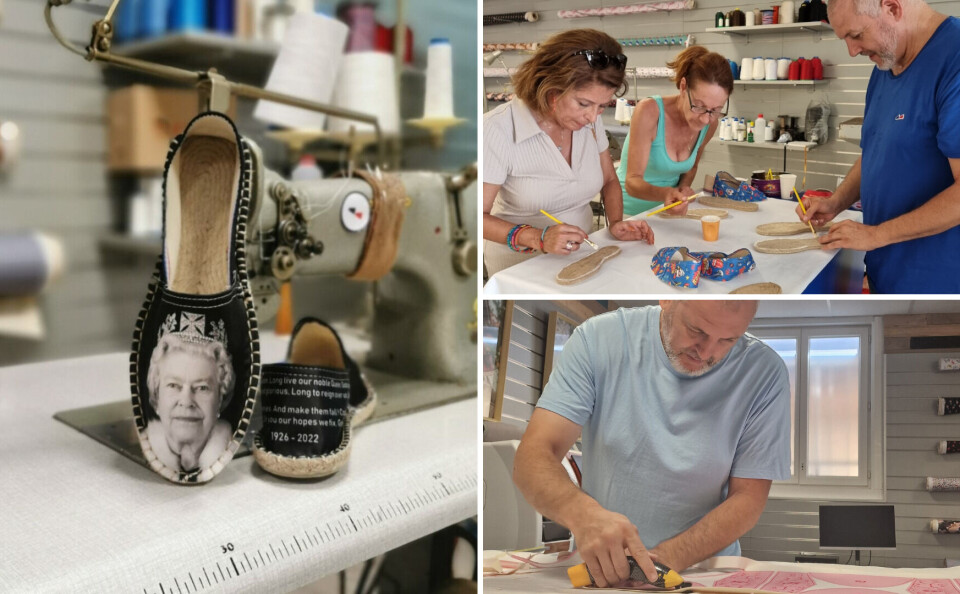
Call Mourad Dembri a couturier and he will probably insist he is nothing of the sort.
“I use sewing techniques and I know how to sew but I am more of a machinist,” he said.
Mr Dembri is workshop supervisor for Payote, which designs, assembles and sells espadrilles.
The firm was recently splashed over the French media after receiving an explosion of orders for its eye-catching espadrille tribute to Queen Elizabeth II.
You might have seen them in magazines, but it is unlikely you are wearing a pair since only 500 of the limited edition were made in the company’s 150m² workshop in Mauléon, Pyrénées-Atlantiques.
Espadrille heartland
Payote is based in south-west France’s espadrille heartland.
The footwear originated in the 14th century in nearby Catalonia, where espadrilles (espardenyas, to give them their ancient Catalan name) were worn by soldiers, peasants and anyone in need of cheap, practical shoes.
The word derives from esparto, the Mediterranean grass traditionally used to make their braided soles.
Over time, however, the industry slowly transitioned to jute to cut costs and, as a result, mass production shifted to Bangladesh, the world’s largest jute producer.
Payote has kept espadrille manufacturing close to home, and Mr Dembri said it is immensely satisfying to see each completed pair of shoes.
Manufacturing process
They take from 10 to 15 minutes to assemble, with several Payote employees taking turns at various points on the assembly line, and sell for around €40.
First, however, the firm’s graphic design department comes up with unique prints for the organic cotton canvas, which is dyed with vegetable ink.
The fabric can then be cut to size with hydraulic presses.
The insole of the espadrille is made of rope, which guarantees comfort and durability.
The outer sole, however, is flat, and formed from recycled vulcanised rubber.
Canvas uppers – what Mr Dembri calls a chausson or tige – are glued on to the soles to complete the espadrille.
Sewing
He then starts sewing the seam à l’italienne, a technique borrowed from Italian fashion designers with one thread coming from the top and another from the bottom with a bobbin.
“This is the most enjoyable part of the process because you really see the espadrille taking shape,” he said.
However, it is also the slowest part. Payote is capable of producing only 100 espadrilles a day by using machinists in this way.
The total would jump to 1,000 if the company focused solely on the processes up to this point.
Nevertheless, Mr Dembri said the effort is worth it, producing a much stronger seam than can be found on other espadrilles from different workshops.
‘Every day is different’
Despite being in the job for more than two years now, Mr Dembri still gets a thrill coming to work.
“Every day is different,” he said.
He fell into the role by chance, having run his own rugby shirt business in Perpignan for 15 years before.
Through this, he already knew Payote’s CEO Olivier Gelly professionally.
When the Covid pandemic struck, Mr Gelly came knocking on his door for fabric to create masks to support the health industry. The pair worked twice a week for three months from 7:00 to 21:00, and sometimes as late as 1:00.
It was only a matter of time before Mr Gelly officially offered Mr Dembri a position in his burgeoning espadrille workshop.
Training and demand
Mr Dembri learned on the job, but formal training exists after completing a Certificat d’aptitude professionnelle (CAP) in carpentry, cabinet-making or locksmithing.
Mr Dembri trains incoming machinists on every step of the espadrille process. One has already finished the training, while two more are still being supervised.
Rising transport costs and a growing focus on making things locally have convinced Mr Dembri that France needs more machinists over the coming years.
“I hope there will be many Mourad Dembris in the future. Machinists are essential-workers,” he said.
He may be right: demand for espadrilles is certainly high.
Payotte says it has had orders in the past numbering in the millions, including from supermarket giants E Leclerc and Monoprix, as well as flagship carrier Air France.
The company is currently looking to expand, eyeing a plot of land to build a much larger 1,500m² factory capable of producing one million espadrilles a year.
Related articles
Discover this French cobbler’s Harry Potter-esque workshop
Historic French shoe brand Paraboot struggles to meet Instagram demand
Two centuries of French glasses, from functional to high fashion