-
Visitors to Normandy American Cemetery must soon book in advance
With more than one million visitors last year, the cemetery is one of the region’s most-visited D-Day sites
-
Easter traditions across France: From rattles and hooded processions to giant omelettes
Regional Pâques celebrations highlight France’s cultural diversity
-
Photos: 94 chateaux open their doors to visitors in Dordogne
The fifth Chateaux en Fête festival offers a chance to look around many impressive properties that are usually private
Do you have Breton 'name bowls'? Here is how they are made
These bowls have become a staple of French cabinets and breakfast tables
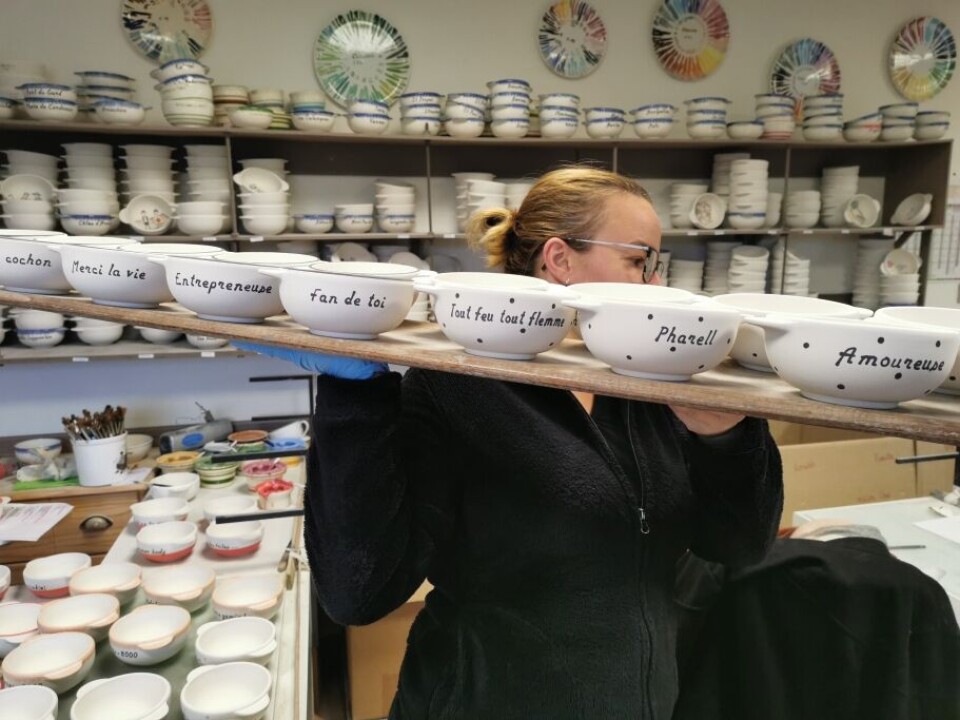
What French people wrongly refer to as a bol breton (bowl from Brittany), edged in blue and with a handle on each side, is actually called a bol à prénom (bowl with a name).
It originated a few hundred kilometres south in the Vendée.
Since production began there in the 1930s, these characterful bowls have become a staple of French cabinets and breakfast tables – often used for hot chocolate for children – and have travelled across the world.
Family members generally have their own, with each bowl bearing a first name on the outside and a motif inside.
Globalisation has forced many manufacturers to outsource production overseas, turn to other activities or shut down completely, but the Cado family, owners of the Nistar company, are among the last in the industry to produce bowls that are handmade at each stage of production.
They bought the original factory of Yves and Marcel Boutain in 2002. These brothers were the first to add names to traditional Breton bowls when, in 1936, they turned the family-owned shop into a ceramics workshop in Saint-Gilles-Croix-de-Vie, a small town on the Atlantic coast south west of Nantes.
These days, the Cado family runs a healthy business, having evolved from the original blue bowl and limited painting variations to offer every name or phrase imaginable, a handful of different colours, and more diverse regional motifs than those popularised in Brittany, where bols à prénom spread.
“The manufacturing process is very long,” said Claude Cado, 74, co-owner of the 850m² Nistar factory.
It starts with a piece of clay that is shaped into a bowl and left to dry for several weeks.
Next comes what is known as ébavurage, a technique aimed at neatening any rough edges to give the bowl a smooth shape, before the handles are attached.
The bol à prénom became known as a bol breton because so many of them were produced in factories in Brittany in the 1950s. Pic: Nistar
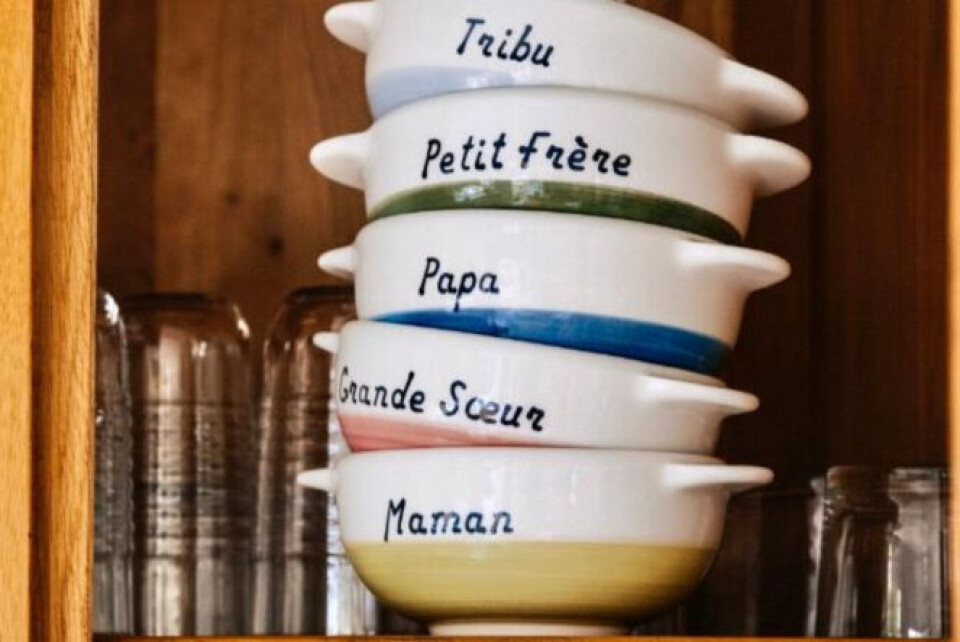
The bowl is then fired at 1,000C for eight hours and left to cool for 36 hours before designs can be painted on to the bottom and side of the bowl in a process known as émaillage (glazing).
Afterwards, the bowl is fired for a second time at 1,050C.
Mr Cado said other companies now outsource a lot of production to China, North Africa, Spain and Portugal, and use transfer printing for the designs rather than doing it by hand, because it is cheaper.
“People are no longer interested in the craft, although it is fascinating,” said Mr Cado.
The bowls used to be made with a distinctive red clay from a nearby family-owned quarry.The Boutain brothers initially produced two types of bowls, one with and one without handles – called oreilles (ears) in French. When the bowl with handles grew popular, they ditched the other model and concentrated on these.
The first bowl was called ‘Ninette’.
Mr Cado said the bol à prénom eventually became known as a bol breton because so many of them were produced in factories in Brittany in the 1950s, and because the Boutain brothers were not involved in marketing.
No intellectual property patent was filed, leaving other firms free to copy the bowl or make their own versions.
Nowadays, Nistar’s administrative operations are run by Stéphanie Cado with father Claude and wife Nelly Cado helping out in production.
Arnaud Cado, Stephanie’s brother, oversees the manufacturing process.
He graduated from the Manufacture et Musée nationaux in Sèvres, Hauts-de-Seine, one of the principal European porcelain factories and the only establishment left in France to teach the craft.
Personalisation has also become key to the company’s survival. Pic: Nistar
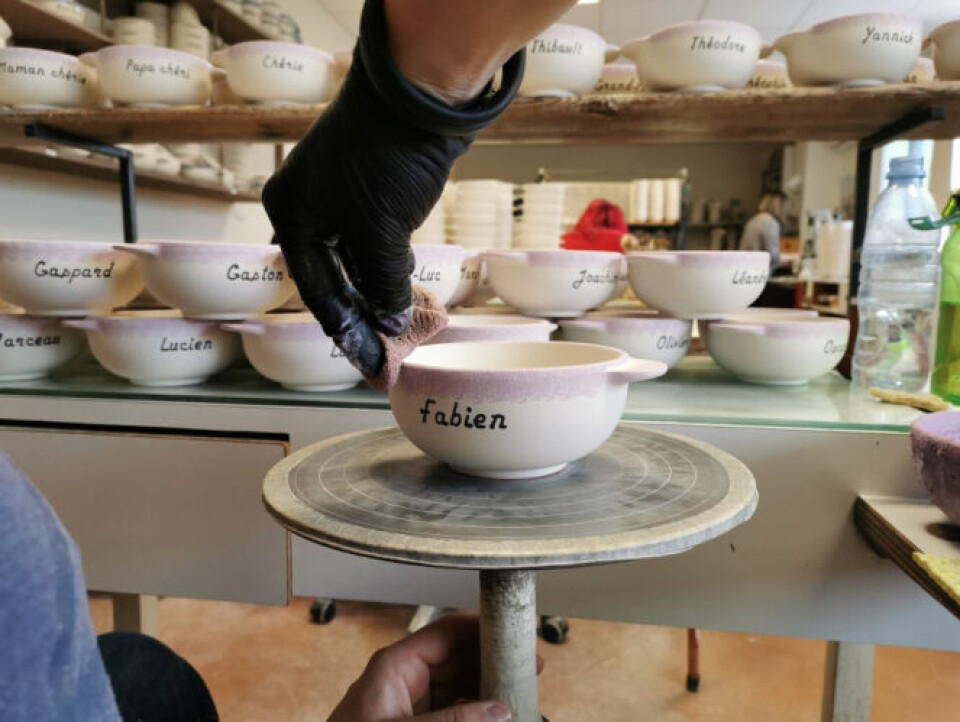
Nistar employs four other workers – three to help with painting and one assisting Arnaud Cado in production.
The variety of bowls has grown from the blue-layered ‘Ninette’ to feature yellow, red, pink and green.
Designs have similarly multiplied from depictions of the traditional bigouden headdress – the tall lace bonnet worn by Breton women – to include scenes such as the Eiffel Tower and Notre-Dame.
Personalisation has also become key to the company’s survival.
“There are countless different spellings of names like Thibaud or Matteo,” said Mr Cado.
He said Emma and Jade were among the most popular female names, with Benjamin and Nathan for their male counterparts.
Nistar even produces bowls with phrases such as ‘I love you Dad/Mum’ or pet names for lovers such as choupinette and ma grosse caille, from €9.80.
The company produces 80,000 handmade bowls a year, or 2,000 bowls a week.
“There are few opportunities to breathe,” Stéphanie Cado admitted.
The Faïencerie Henriot in Quimper and the Faïencerie de Pornic are two other renowned producers of these bowls.
Nistar hopes to obtain the Entreprise du patrimoine vivant status – an official label given by the state to companies to acknowledge excellence in specific crafting skills – but the process is “very, very long”, said Ms Cado.
Related stories:
Discover this French cobbler’s Harry Potter-esque workshop
Makhilas: Discover traditional Basque walking sticks made in France
Art of trimmings: The artisans who supplied French and Monaco royals